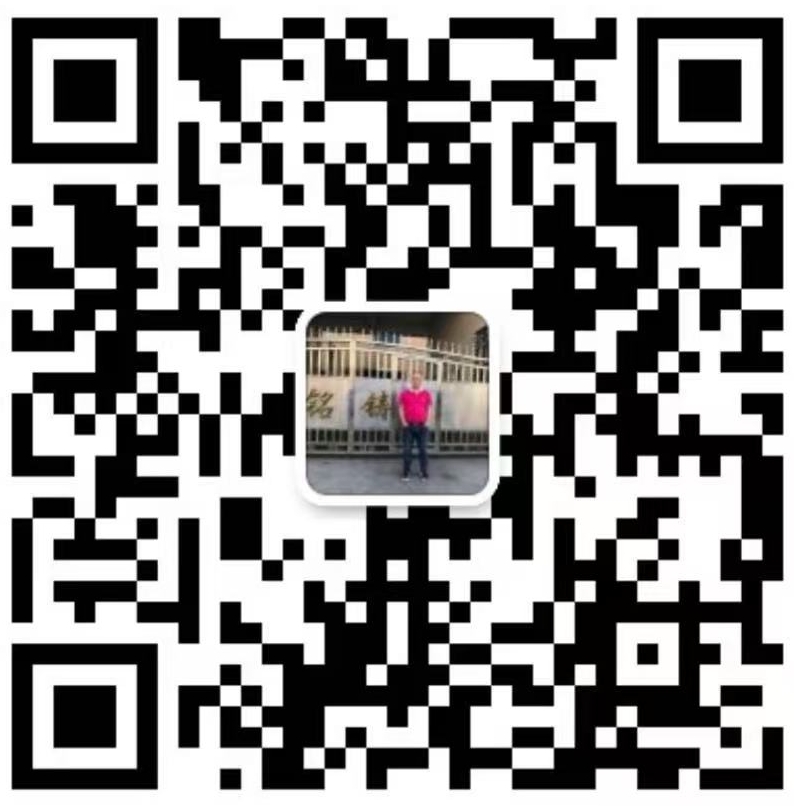
Aluminum alloy die-casting for lighting fixtures
Carefully selected materials:
Made of aluminum alloy, it meets the standard of excellent conductivity, heat transfer, and corrosion resistance
Exquisite workmanship:
Stable structure, polished and polished without burrs, smooth surface without cracks
Professional production:
Strictly follow the technical requirements to ensure the strength and accuracy of the product
Learn moreAluminum alloy die-casting for lighting fixtures
Carefully selected materials:
Made of aluminum alloy, it meets the standard of excellent conductivity, heat transfer, and corrosion resistance
Exquisite workmanship:
Stable structure, polished and polished without burrs, smooth surface without cracks
Professional production:
Strictly follow the technical requirements to ensure the strength and accuracy of the product
Learn moreDie casting molds
Die casting molds
1. Design: Based on the shape, size, and requirements of the product, design the mold cavity, core, pouring system, ejection mechanism, and other structures.
2. Material selection: Choose suitable mold materials based on the type and performance requirements of the die cast metal, such as high-strength alloy steel, heat-resistant steel, etc.
3. Processing: Advanced processing technologies such as CNC machining, electrical discharge machining, and wire cutting are used to accurately process various components of the mold.
4. Heat treatment: The mold is subjected to heat treatment processes such as quenching and tempering to improve its hardness, strength, and wear resistance.
5. Surface treatment: Improve the surface quality and corrosion resistance of the mold through surface treatment processes such as spraying and chrome plating.
6. Assembly and debugging: Assemble the processed mold components, debug and test them to ensure that the performance and quality of the mold meet the requirements.
Learn moreDie casting molds
1. Design: Based on the shape, size, and requirements of the product, design the mold cavity, core, pouring system, ejection mechanism, and other structures.
2. Material selection: Choose suitable mold materials based on the type and performance requirements of the die cast metal, such as high-strength alloy steel, heat-resistant steel, etc.
3. Processing: Advanced processing technologies such as CNC machining, electrical discharge machining, and wire cutting are used to accurately process various components of the mold.
4. Heat treatment: The mold is subjected to heat treatment processes such as quenching and tempering to improve its hardness, strength, and wear resistance.
5. Surface treatment: Improve the surface quality and corrosion resistance of the mold through surface treatment processes such as spraying and chrome plating.
6. Assembly and debugging: Assemble the processed mold components, debug and test them to ensure that the performance and quality of the mold meet the requirements.
Learn moreDie casting molds
Die casting molds
Die casting molds
1. Design: Based on the shape, size, and requirements of the product, design the mold cavity, core, pouring system, ejection mechanism, and other structures.
2. Material selection: Choose suitable mold materials based on the type and performance requirements of the die cast metal, such as high-strength alloy steel, heat-resistant steel, etc.
3. Processing: Advanced processing technologies such as CNC machining, electrical discharge machining, and wire cutting are used to accurately process various components of the mold.
4. Heat treatment: The mold is subjected to heat treatment processes such as quenching and tempering to improve its hardness, strength, and wear resistance.
5. Surface treatment: Improve the surface quality and corrosion resistance of the mold through surface treatment processes such as spraying and chrome plating.
6. Assembly and debugging: Assemble the processed mold components, debug and test them to ensure that the performance and quality of the mold meet the requirements.
Learn moreDie casting molds
Die casting molds
Die casting molds
1. Design: Based on the shape, size, and requirements of the product, design the mold cavity, core, pouring system, ejection mechanism, and other structures.
2. Material selection: Choose suitable mold materials based on the type and performance requirements of the die cast metal, such as high-strength alloy steel, heat-resistant steel, etc.
3. Processing: Advanced processing technologies such as CNC machining, electrical discharge machining, and wire cutting are used to accurately process various components of the mold.
4. Heat treatment: The mold is subjected to heat treatment processes such as quenching and tempering to improve its hardness, strength, and wear resistance.
5. Surface treatment: Improve the surface quality and corrosion resistance of the mold through surface treatment processes such as spraying and chrome plating.
6. Assembly and debugging: Assemble the processed mold components, debug and test them to ensure that the performance and quality of the mold meet the requirements.
Learn moreShaver zinc alloy die-casting
Carefully selected materials:
Made of zinc alloy, it meets the standard for excellent conductivity, heat transfer, and corrosion resistance
Exquisite workmanship:
Stable structure, polished and polished without burrs, smooth surface without cracks
Professional production:
Strictly follow the technical requirements to ensure the strength and accuracy of the product
Learn more